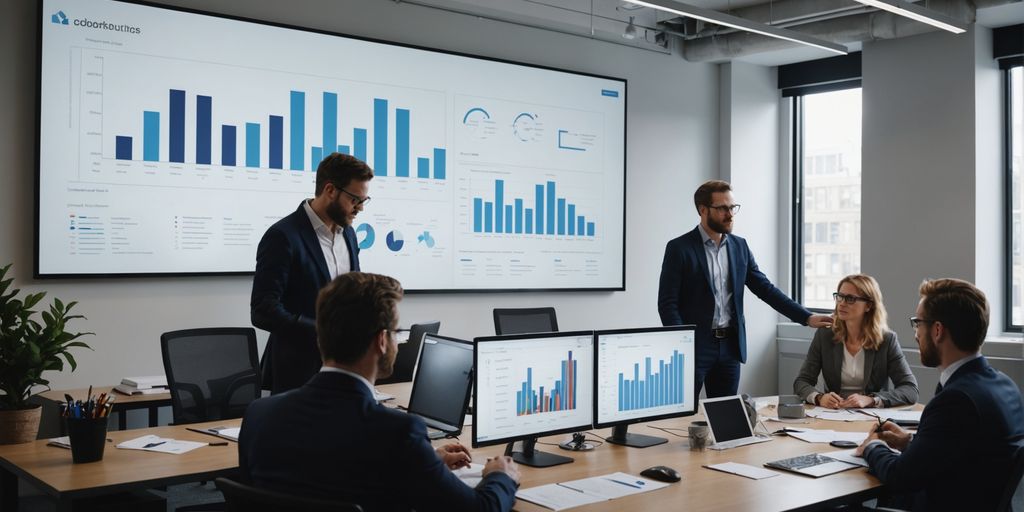
Mastering Operations Improvement: Strategies for Success
Improving operations is key for any business aiming for success. This article explores various strategies to enhance operational efficiency. From understanding core principles to leveraging advanced technologies, we cover essential aspects to help your business thrive.
Key Takeaways
- Aligning operations with business goals ensures unified direction and better efficiency.
- Lean and Six Sigma methodologies are essential for reducing waste and improving quality.
- Technology, including automation and AI, plays a crucial role in achieving operational excellence.
- Overcoming resistance to change and managing integration complexities are vital for successful operations improvement.
- Regularly measuring performance and adapting strategies based on feedback ensures continuous improvement.
Key Principles of Operations Improvement
Understanding Operational Efficiency
Operational efficiency is all about doing more with less. We need to focus on reducing waste and maximizing resources. Efficiency isn’t just a goal; it’s a necessity. By streamlining processes, we can cut down on unnecessary steps and make our operations smoother.
Aligning with Business Objectives
Our operations should always support our business goals. This means aligning our processes with what the business needs to succeed. When we do this, we ensure that every action we take is driving us towards our larger objectives.
Continuous Process Evaluation
Continuous improvement is at the heart of operations improvement. We must constantly evaluate our processes to find areas for enhancement. This isn’t a one-time task but an ongoing effort. By regularly reviewing and tweaking our processes, we can stay ahead of the curve and keep improving.
Implementing Lean and Six Sigma Methodologies
Principles of Lean Management
Lean management focuses on reducing waste and improving processes. By eliminating unnecessary steps, we can make our operations more efficient. Lean principles help us streamline workflows and enhance productivity.
Six Sigma Techniques
Six Sigma aims to improve quality by identifying and removing the causes of defects. It uses data and statistical analysis to enhance process control. This methodology helps us achieve consistent and high-quality results.
Integrating Lean and Six Sigma
Combining Lean and Six Sigma methodologies can drive continuous improvement in our organization. This integrated approach allows us to leverage the strengths of both methods, leading to better efficiency and quality. By adopting these strategies, we can create a culture of continuous improvement and operational excellence.
Leveraging Technology for Operational Excellence
Role of Automation in Operations
Automation is a game-changer for operational excellence. By automating repetitive tasks, we can free up resources to focus on more strategic activities. This not only speeds up processes but also reduces errors and increases accuracy. Imagine a world where manual efforts are minimized, and efficiency is maximized—automation makes this possible.
Utilizing Data Analytics
Data analytics is like having a crystal ball for your business. By analyzing data, we can uncover patterns and insights that help us make better decisions. This means we can predict trends, identify bottlenecks, and optimize our operations. In short, data analytics turns raw data into actionable insights, driving operational excellence.
Adopting AI and Machine Learning
Artificial Intelligence (AI) and Machine Learning (ML) are revolutionizing the way we operate. These technologies can learn from data and make decisions faster than any human. By adopting AI and ML, we can automate complex tasks, improve decision-making, and enhance overall efficiency. It’s like having a super-smart assistant that never sleeps.
By incorporating automation, data analytics, and cloud-based solutions, organizations can significantly improve their workflows, reduce costs, and ultimately achieve operational excellence.
Overcoming Challenges in Operations Improvement
Addressing Resistance to Change
Change is often met with resistance, which can slow down or even derail our efforts. Clear communication about the benefits and alignment with business goals is crucial. Involving employees in the process and providing necessary training can help ease the transition.
Managing Integration Complexities
Integrating new processes or technologies can be daunting. We can tackle this by implementing pilot programs and phased rollouts. This approach allows for gradual adjustments and learning curves, making the process smoother.
Ensuring Stakeholder Engagement
Engaging stakeholders early and often is key to overcoming challenges. Regular updates, open communication, and addressing concerns promptly can build trust and ensure everyone is on the same page.
Continuous monitoring and evaluation are like a safety net, catching problems before they grow.
Measuring Success in Operations Improvement
Setting Key Performance Indicators (KPIs)
To measure success in operations improvement, we need to set clear Key Performance Indicators (KPIs). These KPIs help us track progress and identify areas for enhancement. Some common KPIs include:
- Customer satisfaction scores
- Defect rates
- On-time delivery
- Process cycle time
- Employee productivity
Regular Performance Reviews
Regular performance reviews are essential to ensure we are on the right track. By scheduling quarterly or bi-annual assessments, we can keep our improvement initiatives on track. These reviews help us understand if our strategies are working or if we need to make adjustments.
Continuous monitoring and evaluation are like a safety net, catching problems before they grow.
Adapting Strategies Based on Feedback
Feedback is crucial for continuous improvement. We should implement feedback loops from employees, customers, and stakeholders to ensure our initiatives align with the organization’s needs. If something isn’t working, the data will tell us. This way, we can adjust our strategies and keep improving.
Future Trends in Operations Improvement
Emerging Technologies
In the world of operations improvement, emerging technologies are game-changers. Companies are increasingly adopting tools like robotic process automation (RPA) and adaptive case management to streamline workflows. These technologies not only enhance efficiency but also provide real-time data insights, enabling better decision-making.
Sustainable Practices
Sustainability is no longer just a buzzword; it’s a necessity. Businesses are focusing on sustainable practices to reduce their environmental footprint. This includes everything from optimizing energy use to adopting eco-friendly materials. Sustainable operations not only help the planet but also improve a company’s reputation and bottom line.
Globalization and Its Impact
Globalization continues to shape the landscape of operations improvement. Companies must adapt to different regulations, cultures, and market demands. This often involves leveraging technology to manage complex global supply chains and ensure compliance with local laws. The ability to quickly adapt to these changes can provide a significant competitive edge.
The future of operations improvement is bright and full of potential. As technology advances, businesses must stay ahead of the curve to remain competitive. At Lionheart Business, we are dedicated to helping you navigate these changes and optimize your operations for success. Visit our website to learn more about how we can help you achieve your goals.
Conclusion
Mastering operations improvement is a journey that requires dedication, strategic planning, and continuous adaptation. By focusing on aligning operations with business goals, leveraging technology, and fostering a culture of continuous improvement, organizations can achieve significant gains in efficiency and customer satisfaction. Remember, the key to success lies in the details—monitoring progress, making data-driven decisions, and being agile enough to adapt to changing conditions. With the right strategies in place, businesses can not only meet but exceed their operational goals, paving the way for long-term success.
Frequently Asked Questions
What is operations improvement?
Operations improvement is the process of making a company’s day-to-day activities more efficient and effective. This can involve streamlining processes, reducing waste, and using new technologies to improve performance.
Why is operational efficiency important?
Operational efficiency is crucial because it helps businesses save time and money. When a company runs smoothly, it can produce goods or provide services faster and at a lower cost, leading to higher customer satisfaction and increased profits.
What are Lean and Six Sigma methodologies?
Lean and Six Sigma are methods used to improve business processes. Lean focuses on reducing waste and speeding up processes, while Six Sigma aims to improve quality by identifying and removing the causes of defects.
How can technology improve operations?
Technology can improve operations by automating repetitive tasks, analyzing data for better decision-making, and using AI and machine learning to predict trends and optimize processes. This leads to faster, more accurate, and cost-effective operations.
What are some common challenges in operations improvement?
Common challenges include resistance to change from employees, difficulties in integrating new systems with existing ones, and ensuring that all stakeholders are on board and engaged in the process.
How do you measure success in operations improvement?
Success in operations improvement can be measured using Key Performance Indicators (KPIs), regular performance reviews, and feedback from employees and customers. By tracking these metrics, companies can see where they are improving and where they need to make further changes.