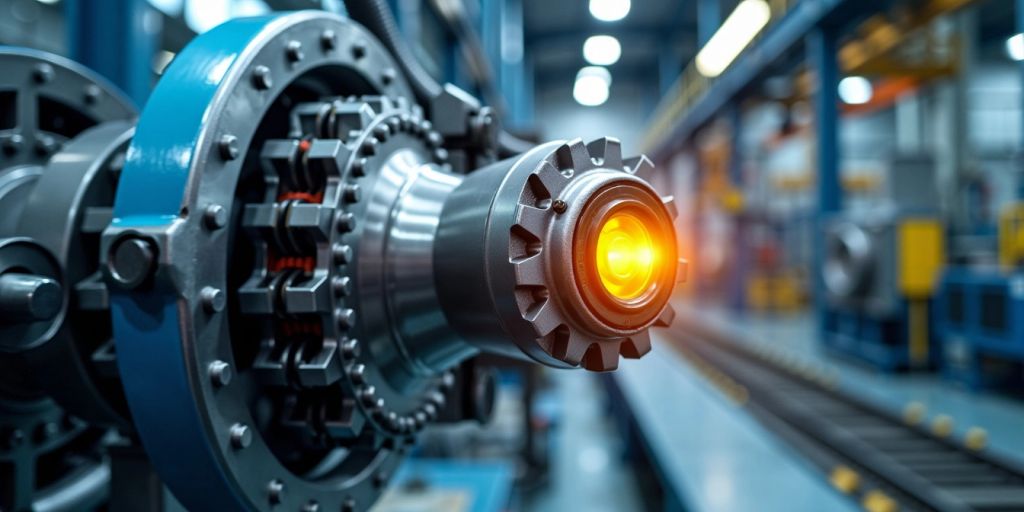
Unlocking Efficiency: The Future of Predictive Maintenance in Industry
Predictive maintenance is changing how industries manage their equipment. Instead of waiting for machines to break down, companies can now use data to foresee problems before they happen. This approach not only saves money but also makes operations smoother and safer. As technology advances, the future of predictive maintenance looks bright, promising even greater efficiency and sustainability in various sectors.
Key Takeaways
- Predictive maintenance uses data to predict equipment failures before they occur.
- This approach can cut downtime by up to 50%, boosting productivity.
- It enhances safety by identifying potential hazards in advance.
- Sustainable practises are supported by reducing unnecessary resource use.
- Industries like aerospace and energy are already benefiting from these strategies.
The Evolution of Predictive Maintenance in Industry
Historical Context and Traditional Approaches
In the past, maintenance strategies were primarily reactive or preventive. We often waited for equipment to fail before taking action, leading to costly downtimes. This traditional approach was not only inefficient but also risky, as it could compromise safety and productivity.
The Shift to Predictive Strategies
As we’ve progressed, the industry has seen a significant shift towards predictive maintenance. This strategy allows us to anticipate equipment failures before they happen, transforming how we manage assets. By using data from sensors, we can now predict when maintenance is needed, rather than relying on fixed schedules. This evolution is crucial as manufacturing becomes more sophisticated, moving from downtime to uptime.
Key Drivers of Change
Several factors have driven this change in maintenance strategies:
- Technological advancements: The rise of IoT and data analytics has made it easier to monitor equipment health in real-time.
- Cost efficiency: Predictive maintenance can reduce unplanned downtimes by up to 50%, leading to significant savings.
- Safety improvements: By identifying potential issues early, we can enhance workplace safety and reduce risks associated with equipment failures.
Predictive maintenance is not just a trend; it’s a necessary evolution in how we approach industrial operations.
In summary, the evolution of predictive maintenance marks a pivotal shift in our industry, enabling us to operate more efficiently and safely than ever before.
Technological Foundations of Predictive Maintenance
Role of Sensors and IoT
In today’s industrial landscape, sensors and the Internet of Things (IoT) are at the heart of predictive maintenance. These technologies allow us to gather real-time data from machinery, enabling us to monitor their condition continuously. By using sensors, we can track various parameters such as temperature, vibration, and pressure, which helps us understand the health of our equipment better. This shift from time-based maintenance to a condition-based approach allows us to perform maintenance precisely when needed, rather than on preset schedules.
Machine Learning and AI Integration
Integrating machine learning and artificial intelligence (AI) into predictive maintenance is a game-changer. These technologies help us analyse vast amounts of data quickly and accurately. With AI, we can identify patterns that might indicate potential failures, allowing us to act before issues escalate. This proactive approach not only saves time but also reduces costs associated with unexpected breakdowns.
Data Analytics and Real-Time Monitoring
Data analytics plays a crucial role in predictive maintenance. By analysing the data collected from sensors, we can gain insights into equipment performance and predict when maintenance is required. Real-time monitoring ensures that we are always aware of our machinery’s condition, enabling us to make informed decisions. Here are some key benefits of data analytics in predictive maintenance:
- Improved decision-making: Access to real-time data helps us make timely and informed choices.
- Cost savings: By predicting failures, we can avoid costly downtime and repairs.
- Enhanced safety: Early detection of potential issues contributes to a safer working environment.
In essence, the combination of sensors, AI, and data analytics is revolutionising how we approach maintenance in industry, making it more efficient and effective than ever before.
Benefits of Predictive Maintenance for Industrial Operations
Enhancing Operational Efficiency
Predictive maintenance is a game-changer for us in the industry. By continuously monitoring machinery, we can predict failures and schedule repairs during planned downtime. This means less disruption and more productivity. Here’s how it helps:
- Minimises unplanned downtime: We can address issues before they become serious, keeping our operations running smoothly.
- Optimises maintenance schedules: Maintenance can be done when it’s most convenient, not just on a set timetable.
- Reduces costs: By preventing major breakdowns, we save money on repairs and replacements.
Reducing Downtime and Costs
The financial benefits of predictive maintenance are significant. We’ve seen reductions in maintenance costs and overall operational expenses. Here’s a quick look:
Benefit | Impact |
---|---|
Reduced unplanned downtime | Up to 50% decrease |
Lower maintenance costs | Significant savings over time |
Increased equipment lifespan | Prolonged asset life |
Improving Safety and Reliability
Safety is paramount in our operations. Predictive maintenance not only enhances reliability but also ensures a safer work environment. By identifying potential hazards early, we can:
- Prevent accidents: Early detection of issues means we can fix them before they cause harm.
- Ensure compliance: Keeping equipment in top shape helps us meet safety regulations.
- Boost employee morale: A safer workplace leads to happier, more productive workers.
Predictive maintenance is not just about saving money; it’s about creating a safer and more efficient workplace for everyone.
Sector-Specific Applications of Predictive Maintenance
In our exploration of predictive maintenance, we find that its applications vary significantly across different industries. This strategy is transforming how sectors operate, enhancing efficiency and reliability.
Aerospace Industry
In the aerospace sector, predictive maintenance is vital for ensuring the safety and reliability of aircraft. By anticipating potential engine issues, airlines can address maintenance needs before they escalate, minimising the risk of in-flight disruptions. Key benefits include:
- Enhanced safety through early detection of issues.
- Improved reliability of aircraft components.
- Reduced maintenance costs by preventing major repairs.
Energy Sector
The energy sector relies heavily on predictive maintenance to prevent equipment failures that could lead to widespread blackouts. By continuously monitoring critical assets, energy providers can implement targeted maintenance interventions. This results in:
- Increased system resilience.
- Lower operational costs.
- Enhanced reliability of power supply.
Oil and Gas Industry
In the oil and gas industry, predictive maintenance helps detect potential risks, such as pipeline leaks, before they escalate. This proactive approach not only protects the environment but also safeguards financial interests. Benefits include:
- Minimised environmental impact.
- Reduced risk of costly emergencies.
- Improved operational efficiency.
Predictive maintenance is not just a trend; it’s a necessity for modern industries to thrive.
In summary, predictive maintenance is making a significant impact across a variety of sectors, as we explore in our article on predictive maintenance examples from 6 different industries. Each sector benefits uniquely, showcasing the versatility and importance of this approach in today’s industrial landscape.
Challenges and Solutions in Implementing Predictive Maintenance
Technical and Operational Barriers
Implementing predictive maintenance strategies can be a transformative process for businesses. However, it also comes with a variety of challenges. One of these is the initial technical complexity. Many companies face difficulties in integrating diverse systems and ensuring that data flows smoothly between them. This can lead to inconsistent data, which is crucial for making informed decisions.
Workforce Skills and Training
Another significant hurdle is the need for a skilled workforce. Predictive maintenance requires knowledge in areas like data analytics and machine learning. To tackle this, we must invest in training programmes that help our teams develop the necessary skills. Here are some steps we can take:
- Upskill existing employees through workshops and hands-on training.
- Attract new talent by offering competitive packages and career development opportunities.
- Implement certification programmes to validate skills and knowledge.
Strategic Partnerships and Collaborations
To overcome these challenges, forming strategic partnerships can be beneficial. Collaborating with technology providers can help us access the latest tools and expertise. By embracing innovation and working together, we can unlock the full potential of predictive maintenance.
By addressing these challenges head-on, we can ensure that our predictive maintenance initiatives are successful and sustainable in the long run.
Future Trends in Predictive Maintenance
Advancements in AI and Machine Learning
As we look ahead, the role of AI and machine learning in predictive maintenance is set to expand significantly. These technologies allow us to analyse vast amounts of data quickly, helping us to identify patterns and predict equipment failures with greater accuracy. This means we can make smarter decisions about when to perform maintenance, ultimately saving time and money.
Integration with Industry 4.0
The integration of predictive maintenance with Industry 4.0 is another exciting trend. By connecting our machines to the internet, we can gather real-time data that enhances our understanding of equipment performance. This connectivity enables us to monitor systems remotely, making it easier to address issues before they escalate.
Emerging Technologies and Innovations
We are also witnessing the rise of cloud-based solutions that offer scalable and cost-effective predictive maintenance options. These platforms allow us to access advanced analytics and machine learning tools without heavy upfront investments. This flexibility is crucial for businesses looking to optimise their maintenance strategies.
The future of predictive maintenance is bright, with innovations paving the way for more efficient and reliable operations.
In summary, the future of predictive maintenance is characterised by:
- Enhanced AI and machine learning capabilities
- Seamless integration with Industry 4.0
- Adoption of cloud-based solutions for flexibility and scalability
By embracing these trends, we can look forward to a future where maintenance is not just reactive but proactive, leading to significant cost savings and improved operational efficiency.
Sustainability and Predictive Maintenance
Reducing Environmental Impact
Predictive maintenance is not just about keeping machines running; it’s also about being kind to our planet. By using data-driven insights, we can spot inefficiencies early and fix them before they lead to waste. This means less energy consumption and fewer resources used, which is a win for everyone.
Optimising Resource Utilisation
When we adopt predictive maintenance, we can make better use of our resources. Here are some key points to consider:
- Less waste: By fixing issues before they escalate, we reduce the amount of materials thrown away.
- Energy savings: Efficient machines use less energy, which helps lower our carbon footprint.
- Longer equipment life: Taking care of our machines means they last longer, reducing the need for replacements.
Aligning with Global Sustainability Goals
As industries strive to meet sustainability targets, predictive maintenance plays a crucial role. It helps us align with global goals by:
- Minimising emissions through efficient operations.
- Supporting circular economy practises by extending the life of equipment.
- Contributing to a sustainable future by reducing our overall environmental impact.
By embracing predictive maintenance, we’re not just improving our operations; we’re also making a positive impact on the environment.
In conclusion, predictive maintenance is a powerful tool that helps us achieve sustainability in our industrial practises. It’s about being smart with our resources and ensuring a better future for all.
In today’s world, keeping things running smoothly is more important than ever. Predictive maintenance helps businesses avoid unexpected breakdowns and save money on repairs. By using smart technology, companies can spot problems before they happen. If you’re curious about how this can work for you, visit our website to learn more!
Conclusion
In summary, predictive maintenance is changing the way industries manage their equipment. This approach allows companies to foresee problems before they happen, which helps in planning maintenance at the right time. By using smart technology and data analysis, businesses can keep their machines running smoothly, reduce unexpected breakdowns, and save money. As we move forward, the role of predictive maintenance will only grow, making operations more efficient and reliable. Embracing this method not only enhances productivity but also supports a safer and more sustainable working environment.
Frequently Asked Questions
What is predictive maintenance?
Predictive maintenance is a method that uses data from machines to predict when maintenance should be done. This helps to fix problems before they cause breakdowns.
How does predictive maintenance work?
It works by collecting data from sensors on machines. This data is then analysed to find patterns that can indicate when a machine might fail.
What are the benefits of using predictive maintenance?
Using predictive maintenance can reduce unexpected machine failures, lower maintenance costs, and improve overall efficiency in operations.
Which industries benefit most from predictive maintenance?
Industries like aerospace, energy, and oil and gas see significant benefits from predictive maintenance due to the high costs of downtime.
What challenges come with implementing predictive maintenance?
Some challenges include the need for skilled workers, the cost of new technology, and the integration of systems.
What is the future of predictive maintenance?
The future looks bright with advancements in technology like AI and IoT, which will help make predictive maintenance even more effective.