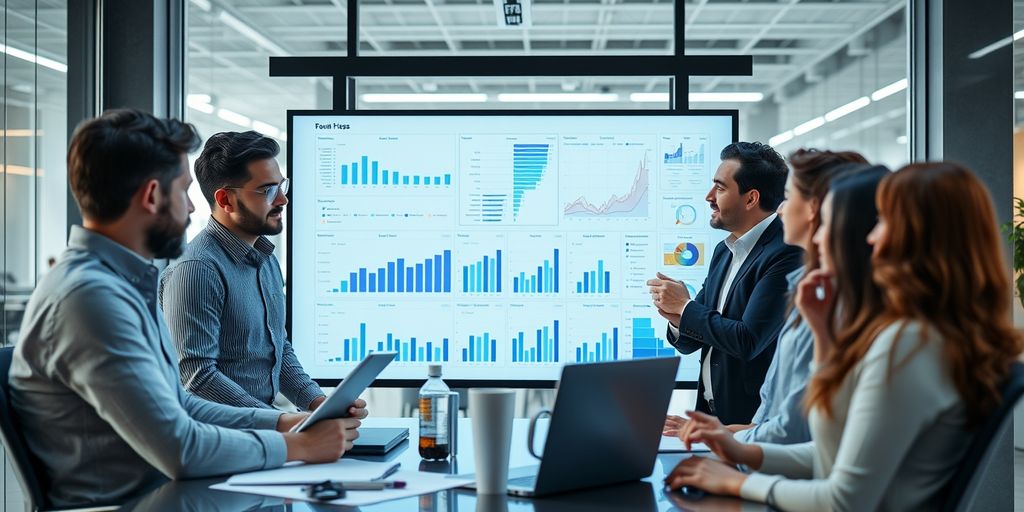
Mastering Business Process Improvement: Strategies for Success
Improving business processes is key to making any company run better. It helps in cutting down waste, boosting productivity, and delivering more value to customers. In this article, we’ll explore the basics of business process improvement and share effective strategies for success.
Key Takeaways
- Understanding the basics of business process improvement is essential for any organization looking to grow.
- Identifying and fixing weak points in current processes can lead to major efficiency gains.
- Choosing the right methods and planning carefully are crucial for successful process improvements.
- Using tools like process mapping and automation can make the improvement process smoother.
- Continuous monitoring and a culture that values improvement help keep processes efficient over time.
Understanding the Fundamentals of Business Process Improvement
Defining Business Process Improvement
Business Process Improvement (BPI) is all about making our business run smoother by optimizing its core processes. We look at what we do now, find ways to do it better, and then make those changes. It’s a way to cut out waste and boost efficiency.
Key Principles and Concepts
There are a few key ideas behind BPI:
- Continuous Improvement: Always look for ways to get better.
- Customer Focus: Make sure changes help our customers.
- Employee Involvement: Get everyone on board with the changes.
The Role of Business Process Management
Business Process Management (BPM) is the bigger picture that includes BPI. BPM helps us discover, map, automate, and manage our processes. It’s like the roadmap for our journey to better business processes.
By understanding and applying these fundamentals, we can make our business more efficient and effective.
Identifying Opportunities for Process Improvement
Analyzing Current Processes
To start, we need to take a close look at our existing processes. This means mapping out each step and understanding how they all fit together. By doing this, we can see where things might be going wrong. It’s like having a roadmap that shows us the way.
Recognizing Inefficiencies and Bottlenecks
Once we have a clear picture of our processes, the next step is to spot the inefficiencies and bottlenecks. These are the areas where things slow down or get stuck. We need to ask ourselves questions like, "Why is this taking so long?" or "Is there a better way to do this?" This helps us identify the opportunity for improvement.
Gathering Stakeholder Feedback
Finally, we need to talk to the people who are involved in these processes. This includes employees, managers, and even customers. Their feedback is crucial because they can provide insights that we might not see. By engaging with stakeholders, we can gather valuable insights into process pain points, challenges, and improvement opportunities.
Identifying opportunities for process improvement is a team effort. By working together and listening to everyone’s input, we can make our processes better and more efficient.
Implementing Effective Process Improvement Strategies
Selecting the Right Methodology
Choosing the right methodology is crucial for successful process improvement. We need to consider various approaches like Lean, Six Sigma, and Total Quality Management (TQM). Each has its strengths and can be tailored to fit our specific needs. Selecting the right methodology ensures that we address the unique challenges of our processes effectively.
Developing a Detailed Plan
Once we’ve chosen a methodology, the next step is to develop a detailed plan. This involves mapping out the current process, identifying areas for improvement, and setting clear, achievable goals. A well-thought-out plan acts as a roadmap, guiding us through each step of the improvement process.
Ensuring Stakeholder Engagement
Engaging stakeholders is essential for the success of any process improvement initiative. We need to involve team members, managers, and other key stakeholders from the beginning. Their input and feedback are invaluable in identifying pain points and developing effective solutions. By ensuring stakeholder engagement, we can foster a sense of ownership and commitment to the improvement process.
Involving stakeholders early on helps in recognizing inefficiencies and bottlenecks, making the improvement process more effective and inclusive.
Tools and Techniques for Business Process Improvement
Process Mapping and Documentation
Creating a visual map of the existing process is a great way to understand how it flows through different departments. This helps us see the various steps and components that run sequentially or in parallel. Process mapping can highlight areas of inefficiency or ineffectiveness that can be improved. By using feedback from stakeholders, we can analyze which steps take the most time, create bottlenecks, or fail to provide value.
Lean and Six Sigma
Lean and Six Sigma are two popular methodologies for process improvement. Lean focuses on identifying and eliminating non-value-adding activities to streamline operations. Six Sigma uses a data-driven approach to improve processes through precise measurements and rigorous analysis. Both methods aim to enhance quality and efficiency.
Automation and Technology Integration
Automation can quickly improve a business process by eliminating manual bottlenecks and addressing repeatability and quality issues. We should determine what resources are available to invest in business process automation software. Automation tools can help us achieve better efficiency and productivity.
By integrating these tools and techniques, we can make our business processes more efficient and effective, ultimately delivering greater value to our customers.
Measuring and Monitoring Process Improvement
Setting Key Performance Indicators (KPIs)
To measure our progress, we need to set clear Key Performance Indicators (KPIs). These KPIs help us understand if our process improvements are working. Choosing the right KPIs is crucial because they show us where we are doing well and where we need to improve. Some common KPIs include cycle time, error rates, and customer satisfaction.
Continuous Monitoring and Feedback Loops
Once we have our KPIs, we need to keep an eye on them. This means continuously monitoring our processes and gathering feedback. By doing this, we can spot any issues early and fix them before they become big problems. Feedback loops are essential for making sure our improvements stick.
Monitoring and feedback are like a safety net, catching problems before they grow.
Adjusting Strategies Based on Data
Data is our best friend when it comes to process improvement. We should use the data we collect to adjust our strategies. If something isn’t working, the data will tell us. This way, we can make informed decisions and keep improving. Remember, measuring continuous improvement metrics can help us enhance processes, reduce costs, and foster a culture of excellence.
Creating a Culture of Continuous Improvement
Creating a culture of continuous improvement starts with strong leadership and clear communication. Leaders must champion the importance of process improvement and empower employees at all levels to actively participate in identifying opportunities for enhancement.
By fostering a collaborative and innovative environment, organizations can encourage employees to share their insights, ideas, and feedback to drive continuous improvement efforts forward.
In addition, providing ongoing training and development opportunities for employees can help build the skills and knowledge needed to effectively analyze processes, implement changes, and measure results. By investing in the professional growth of their workforce, organizations can cultivate a culture of continuous learning and improvement.
Furthermore, recognizing and celebrating successes along the way can help reinforce the value of process improvement efforts and motivate employees to continue striving for excellence. By highlighting the positive impact of their contributions, organizations can inspire a sense of pride and ownership in the improvement process.
Ultimately, creating a culture of continuous business process improvement requires a commitment to transparency, collaboration, and innovation. By fostering a workplace where continuous improvement is not just a goal, but a way of life, organizations can drive sustainable growth and success in the long run.
Overcoming Challenges in Business Process Improvement
Common Obstacles and Pitfalls
When we dive into business process improvement, we often face several common obstacles. These can range from resistance to change, lack of clear communication, to insufficient resources. It’s crucial to identify these pitfalls early on to avoid setbacks.
Strategies for Effective Change Management
To overcome these challenges, we need effective change management strategies. Here are some steps:
- Communicate Clearly: Make sure everyone understands the changes and why they’re necessary.
- Engage Stakeholders: Involve everyone affected by the changes to get their input and buy-in.
- Provide Training: Equip your team with the skills they need to adapt to new processes.
- Monitor Progress: Keep an eye on how the changes are being implemented and make adjustments as needed.
Case Studies and Real-World Examples
Learning from others can be incredibly valuable. For instance, one company managed to overcome the challenges of business process automation by following expert advice. They started with small, manageable changes and gradually scaled up, ensuring each step was thoroughly tested before full implementation.
By addressing these challenges head-on and using proven strategies, we can make our business process improvement efforts more successful and sustainable.
Facing hurdles in improving your business processes? You’re not alone. Many companies struggle with this, but the good news is, solutions are within reach. At Lionheart Business, we specialize in turning these challenges into opportunities for growth. Ready to take the next step? Visit our website and discover how we can help you achieve your goals.
Conclusion
Mastering business process improvement is not just about making small changes; it’s about creating a culture of continuous enhancement. By focusing on streamlining workflows, reducing inefficiencies, and delivering greater value, businesses can achieve sustainable growth. The journey involves strong leadership, clear communication, and active participation from all levels of the organization. Remember, the goal is to make process improvement a part of your company’s DNA. With dedication and the right strategies, your business can thrive in an ever-changing market.
Frequently Asked Questions
What is Business Process Improvement (BPI)?
Business Process Improvement (BPI) is a method to find and fix problems in business processes. The goal is to make things work better and faster by cutting out wasted time and steps.
Why is Business Process Improvement important?
BPI helps businesses run more smoothly. It can save time, reduce costs, and make customers happier by improving how things are done.
How do you identify areas that need improvement?
You can find areas to improve by looking at how things are done now, spotting slow or wasteful steps, and asking workers and customers for their ideas.
What tools can help with Business Process Improvement?
Tools like process maps, Lean, Six Sigma, and automation technology can help make business processes better.
What are Key Performance Indicators (KPIs)?
KPIs are measurements that show how well a process is working. They help you see if changes are making things better.
How can we keep improving after making changes?
After changes are made, keep an eye on the results and ask for feedback. Make new adjustments as needed to keep things running well.