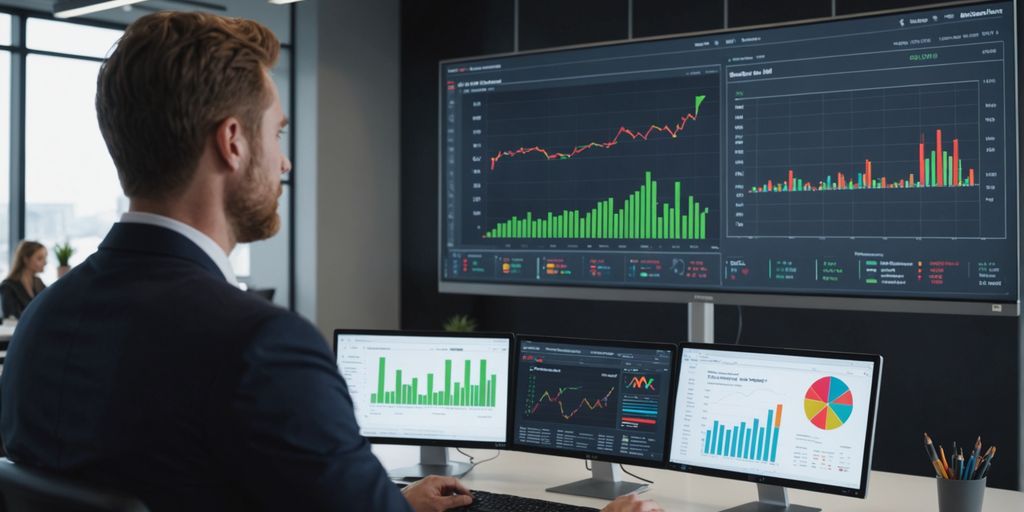
Mastering Strategic Process Optimization: Key Techniques for Business Success
In today’s fast-paced business world, companies need to constantly improve their processes to stay ahead. Mastering strategic process optimization is key to achieving this. By refining workflows and using technology, businesses can boost efficiency and reach their goals faster. This article explores essential techniques for optimizing processes and ensuring business success.
Key Takeaways
- Strategic process optimization helps businesses streamline their operations and improve efficiency.
- Setting clear, measurable objectives is crucial for successful process optimization.
- Integrating suitable technologies like automation and data analytics can significantly enhance process efficiency.
- Employee involvement and continuous training are essential for sustaining process improvements.
- Continuous monitoring and evaluation ensure that optimization efforts remain effective over time.
Understanding the Fundamentals of Strategic Process Optimization
Defining Strategic Process Optimization
Strategic process optimization is all about making our business processes better and more efficient. It’s an iterative process that involves talking to the people it affects and making changes as you go. We look at what we do now, find ways to improve, and then make those changes.
Importance of Strategic Process Optimization in Business
Why is this important? Well, optimizing our processes helps us save time and money. It also makes our work easier and more effective. When we optimize, we can do more with less effort, which is great for everyone involved.
Key Components of Effective Process Optimization
There are a few key parts to making process optimization work:
- Clear Goals: We need to know what we want to achieve.
- Data Analysis: Looking at data helps us see where we can improve.
- Employee Involvement: Getting input from the people who do the work is crucial.
- Technology: Using the right tools can make a big difference.
Remember, optimization is an ongoing journey. We keep improving as we go, making our business better step by step.
Setting Clear Objectives for Process Optimization
Aligning Objectives with Business Goals
First, we need to make sure our optimization goals match our business goals. This means our efforts should help the company in the long run. Whether we want to boost efficiency, cut costs, or improve quality, our goals should fit the big picture.
Defining Measurable Targets
Next, we need to set targets we can measure. This helps us see if we’re making progress. For example, we might aim to reduce the time it takes to complete a task by 20%. Clear targets keep us on track.
Prioritizing Key Areas for Improvement
Finally, we should focus on the most important areas first. Not all processes need fixing right away. By prioritizing, we can tackle the biggest issues that will give us the best results. This way, we can make the most impact with our efforts.
Implementing Technology for Enhanced Efficiency
Identifying Suitable Technologies
When it comes to optimizing processes, technology plays a crucial role. We need to identify the right technologies that fit our business needs. This could include automation tools, data analytics, or machine learning. Each of these can help us streamline operations and improve efficiency.
Integrating Automation and Data Analytics
Automation and data analytics are game-changers. Automation can handle repetitive tasks, freeing up our team to focus on more strategic activities. Data analytics, on the other hand, provides insights that help us make informed decisions. By integrating these technologies, we can enhance our overall productivity.
Ensuring Seamless Technology Adoption
Adopting new technology isn’t just about buying the latest tools. It’s about making sure they fit into our existing processes smoothly. This means planning, training, and continuous monitoring. Our team needs to be comfortable with the new systems to make the most out of them.
Technology helps small business owners improve their customer experience with automated systems and increased personalization.
In summary, leveraging the right technology can significantly boost our efficiency and help us stay competitive in the market.
Employee Involvement and Training
Creating a Culture of Continuous Improvement
To truly master process optimization, we need to create a culture of continuous improvement. This means fostering an environment where employees feel motivated to contribute their ideas and efforts. When everyone is on board, we can achieve amazing results. Recognizing and rewarding contributions can further boost employee engagement and motivation.
Providing Adequate Training
Training is crucial. We must ensure that our team is proficient in any new technologies or processes we introduce. This not only helps in smooth implementation but also empowers employees to take ownership of their roles. Adequate training can make a significant difference in how effectively new systems are adopted.
Encouraging Cross-Functional Collaboration
Encouraging cross-functional collaboration is another key aspect. When different departments work together, we can leverage the collective intelligence of the organization. This collaboration fosters a more innovative and efficient work environment. By breaking down silos, we can ensure that ideas and insights flow freely across the organization.
Creating a culture of continuous improvement is not just about processes; it’s about people. When employees are motivated and well-trained, they become the driving force behind successful process optimization.
Continuous Monitoring and Evaluation
Establishing Key Metrics for Monitoring
To keep our processes running smoothly, we need to set up key metrics. These metrics help us see how well things are going and where we might need to make changes. Establishing key metrics for monitoring is like having a roadmap; it shows us the way and helps us stay on track. Some common metrics include cycle time, error rates, and customer satisfaction.
Creating Feedback Loops
Feedback loops are essential for catching problems early. By gathering feedback from employees and customers, we can spot issues before they become big problems. This continuous monitoring helps us make sure our improvements stick. Think of feedback loops as a safety net, catching problems before they grow.
Iterative Enhancement and Adaptation
Once we have our metrics and feedback, we can use this data to make informed decisions. If something isn’t working, the data will tell us. This way, we can adjust our strategies and keep improving. Iterative enhancement and adaptation are key to staying competitive and efficient. It’s all about making small changes and seeing big results.
Continuous monitoring and evaluation are like a safety net, catching problems before they grow.
Case Studies of Successful Process Optimization
To illustrate the effectiveness of mastering process optimization, examining real-world examples is valuable. Numerous industries have successfully optimized their processes, leading to significant improvements in efficiency. By delving into these case studies, businesses can gain inspiration and insights into how optimization strategies can be tailored to their needs.
Overcoming Challenges in Process Optimization
Addressing Resistance to Change
Resistance to change is a common hurdle in any organizational transformation. To tackle this, we need to communicate effectively and manage change strategically. Clear communication helps everyone understand why changes are necessary. Engaging stakeholders early on can also ease the transition.
Managing Integration Challenges
Integration challenges can be daunting. Implementing pilot programs and phased rollouts can help. This approach allows for gradual adjustments and learning curves, making the process smoother.
Strategies for Sustained Improvement
For sustained improvement, it’s crucial to have a plan. Here are some steps:
- Identify key areas for improvement.
- Set measurable targets.
- Monitor progress regularly.
- Adjust strategies as needed.
By proactively addressing potential obstacles, we can navigate the optimization process more smoothly, ensuring that the benefits outweigh the challenges.
Future Trends in Process Optimization
Role of Artificial Intelligence and Machine Learning
As we look ahead, artificial intelligence (AI) and machine learning (ML) are set to revolutionize process optimization. These technologies can analyze vast amounts of data, identify patterns, and make predictions that help businesses streamline their operations. Imagine a system that learns from every transaction and continuously improves its efficiency—this is the power of AI and ML in action.
Impact of Internet of Things (IoT)
The Internet of Things (IoT) is another game-changer. By connecting devices and systems, IoT provides real-time data and insights, enhancing visibility and control over various processes. For instance, in manufacturing, IoT can monitor equipment health and predict maintenance needs, reducing downtime and increasing productivity.
Environmental and Social Considerations
In today’s world, businesses must also consider environmental and social factors in their optimization efforts. Sustainable practices are not just good for the planet but can also lead to cost savings and improved brand reputation. Companies are increasingly adopting green technologies and ethical practices to meet these demands.
The future of process optimization is exciting, with technologies like AI, ML, and IoT leading the way. Businesses that embrace these trends will be well-positioned to thrive in an ever-evolving landscape.
The future of process optimization is bright and full of potential. As technology advances, businesses must stay ahead of the curve to remain competitive. At Lionheart Business, we are dedicated to helping you navigate these changes and achieve new levels of efficiency. Visit our website to learn more about how we can support your growth and innovation.
Conclusion
Mastering strategic process optimization is not just a one-time effort but a continuous journey that requires dedication and adaptability. By focusing on clear objectives, leveraging the right technologies, and fostering a culture of continuous improvement, businesses can significantly enhance their efficiency and competitiveness. Employee involvement and cross-functional collaboration are crucial, as they bring diverse insights and drive innovation. Continuous monitoring and feedback loops ensure that the optimization efforts remain aligned with the evolving business landscape. Ultimately, the key to successful process optimization lies in the commitment to ongoing evaluation and improvement, enabling businesses to thrive in a dynamic market environment.
Frequently Asked Questions
What is strategic process optimization?
Strategic process optimization is about making business processes work better and more efficiently. It involves analyzing and improving workflows to align with the company’s goals.
Why is strategic process optimization important for businesses?
It’s important because it helps businesses run smoother, save money, and improve customer satisfaction. Better processes lead to better overall performance.
How do you set objectives for process optimization?
To set objectives, you need to align them with your business goals, define clear and measurable targets, and prioritize the key areas that need improvement.
What role does technology play in process optimization?
Technology helps by automating tasks and analyzing data to find inefficiencies. It makes processes faster and more accurate, which boosts overall efficiency.
How can employees contribute to process optimization?
Employees can help by embracing a culture of continuous improvement, getting proper training, and working together across different departments to share ideas and solve problems.
What are some common challenges in process optimization?
Common challenges include resistance to change, difficulties in integrating new processes, and maintaining continuous improvement. Addressing these challenges requires good communication, gradual implementation, and ongoing evaluation.