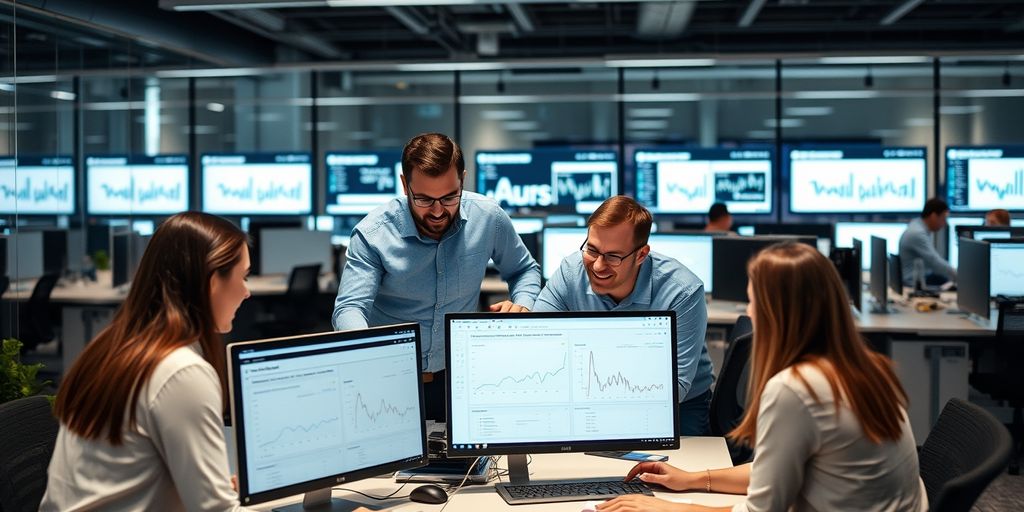
Maximizing Efficiency: Proven Strategies for Operations Improvement
Operational efficiency is the backbone of any successful business. It means doing more with less – more output with less input. This article will explore proven strategies to boost operations, enhance productivity, and improve customer satisfaction. By the end, you’ll have practical tips to make your business run smoother and smarter.
Key Takeaways
- Operational efficiency directly impacts customer satisfaction through faster service, consistent quality, and fewer mistakes.
- Key strategies for improving efficiency include optimizing processes, using technology, and smart resource allocation.
- Real-world examples, like Toyota’s Just-in-Time system, show how efficiency can lead to major cost savings and better performance.
- Technology plays a crucial role in enhancing efficiency by automating tasks, integrating systems, and using predictive analytics.
- Evaluating and scaling successful efficiency initiatives help maintain continuous improvement and long-term benefits.
The Impact of Operational Efficiency on Customer Satisfaction
Operational efficiency directly influences how happy our customers are. When we streamline our processes, we can deliver services faster, maintain consistent product quality, and reduce errors. These factors are crucial for keeping our customers satisfied.
Faster Service Delivery
When we improve our internal processes, we can serve our customers more quickly. For example, a bank that optimizes its loan approval process can provide faster responses to customer applications. This not only makes customers happy but also builds trust and credibility.
Consistent Product Quality
Operational efficiency helps us maintain a consistent level of quality in our products. When we have efficient processes, we can ensure that every product meets the same high standards. This consistency is key to building a strong brand reputation.
Error Reduction
By streamlining our operations, we can significantly reduce the number of errors. Fewer mistakes mean happier customers and fewer complaints. This not only saves us time and resources but also enhances the overall customer experience.
Efficient internal processes often result in faster service delivery, more consistent product quality, and fewer errors – all key factors in customer satisfaction.
Key Strategies for Boosting Operational Efficiency
Process Optimization and Streamlining
First, we need to look at our current workflows. By mapping out these processes, we can spot bottlenecks and inefficiencies. For example, a factory might find that materials are moved too much between stations. Fixing this can save time and money. Another idea is to use a just-in-time inventory system to cut down on storage costs.
Leveraging Technology
Next, we should use technology to our advantage. Automating repetitive tasks can free up our team for more important work. It’s also crucial to make sure our systems are well-integrated. This helps prevent information silos, which can slow us down.
Effective Resource Allocation
Finally, we need to be smart about how we use our resources. This means forecasting demand accurately so we don’t over or underuse our resources. Regular capacity planning can help us adjust our resources as needed. We should also consider cross-training employees to make our workforce more flexible.
Real-World Examples of Successful Operations Improvement
Examining real-world examples of operational efficiency improvements can provide valuable insights and inspiration for organizations seeking to enhance their own operations. These case examples demonstrate how companies across various industries have successfully implemented efficiency measures, leading to significant benefits. Let’s explore some notable examples of operational efficiency in action.
Implementing Technology for Enhanced Operational Efficiency
Automation of Repetitive Tasks
One of the most effective ways to boost operational efficiency is by automating repetitive tasks. Automation frees up human resources to focus on more valuable activities. For example, Robotic Process Automation (RPA) can handle data entry, account reconciliations, and report generation. This not only speeds up processes but also reduces the risk of human error.
Integration of Systems
Integrating various systems ensures smooth data flow and prevents information silos. When systems are well-integrated, it becomes easier to manage resources and make informed decisions. This integration is crucial for maintaining operational efficiency and avoiding bottlenecks.
Utilizing Predictive Analytics
Predictive analytics can significantly enhance operational efficiency by providing real-time data for better decision-making. By analyzing historical data, companies can forecast future trends and make proactive adjustments. This helps in optimizing resources and improving overall productivity.
Studies have shown that companies that invest in technology to streamline processes and enhance efficiency experience significant increases in productivity.
In summary, leveraging technology through automation, system integration, and predictive analytics can lead to substantial improvements in operational efficiency.
Evaluating and Scaling Efficiency Initiatives
Measuring Impact
To understand how well our efficiency initiatives are working, we need to measure their impact. This means tracking key performance indicators (KPIs) and other metrics that show us if we’re hitting our goals. Regular reviews help us see what’s working and what needs tweaking.
Identifying Successful Practices
Once we know what’s working, we can identify successful practices. These are the strategies and methods that have delivered the best results. By pinpointing these, we can focus on what to scale up across the organization.
Scaling Proven Measures
Scaling proven measures is all about taking those successful practices and applying them more broadly. This helps the entire organization benefit from localized successes. Efficient scaling enables us to leverage our existing resources effectively and maintain a competitive edge in the market.
By evaluating and scaling our efficiency initiatives, we ensure that our efforts lead to sustainable improvements and long-term benefits. This approach allows us to continually refine and adapt, which is crucial in today’s rapidly changing business environment.
Effective Resource Allocation and Optimization
Efficient resource allocation and optimization are crucial for maximizing operational efficiency. When resources are allocated effectively, businesses can minimize waste, reduce costs, and improve productivity.
Demand Forecasting
By accurately forecasting demand, businesses can align their resources to meet customer needs effectively. This helps prevent over or underutilization of resources, reducing costs and enhancing operational efficiency.
Capacity Planning
Conducting regular capacity planning exercises allows businesses to assess their resource requirements and adjust accordingly. This ensures that resources, such as labor, equipment, and facilities, are optimized to meet demand and avoid bottlenecks.
Cross-Training Employees
Cross-training employees across different roles or departments enables businesses to utilize their workforce more effectively. This flexibility allows employees to fill in for absent colleagues, adapt to changing demands, and maintain operations without disruptions.
Gaining a Competitive Edge Through Operational Efficiency
Cost Reduction and Resource Optimization
Operational efficiency often reveals ways to cut costs and use resources better. By spotting waste in processes, we can remove unnecessary steps or resources. For example, a logistics company might use route optimization software to plan better delivery routes. This can save on fuel, reduce vehicle wear and tear, and cut down driver hours. These efforts not only improve efficiency but also free up cash, giving us more financial flexibility.
Enhanced Competitiveness
Being efficient helps us stay ahead in the market. It allows us to be more flexible with our pricing, possibly undercutting competitors while still making a profit. Faster production or service delivery can set us apart, especially in industries where speed is key. For instance, a software company that improves its development process can launch new features quicker, meeting customer needs faster and staying ahead of the competition.
Adapting to Market Changes
Efficiency makes us more agile, helping us adapt to market changes swiftly. When we streamline our operations, we can respond to new trends and demands more quickly. This agility is crucial for maintaining a competitive edge in a fast-paced market. By continuously improving our processes, we ensure that we are always ready to meet new challenges and seize opportunities.
Boost your business by improving how you work. When you make your operations smoother, you can get ahead of others. Want to learn more? Visit our website and see how we can help you reach your goals.
Conclusion
Improving operational efficiency is a continuous journey that requires dedication and strategic planning. By focusing on streamlining processes, leveraging technology, and optimizing resources, businesses can achieve significant gains in productivity and cost savings. These improvements not only enhance internal operations but also lead to higher customer satisfaction and a stronger competitive position in the market. Remember, the key to success lies in consistent application, regular evaluation, and a willingness to adapt to changing business environments. With these strategies in place, organizations can look forward to sustainable growth and long-term success.
Frequently Asked Questions
How does operational efficiency affect customer satisfaction?
Operational efficiency leads to faster service, better product quality, and fewer mistakes. This makes customers happier because they get what they want quickly and reliably.
What are some key strategies to improve operational efficiency?
Some key strategies include optimizing processes, using technology, and allocating resources effectively. These methods help businesses run smoother and cut costs.
Can you give an example of a company that improved its operations?
Sure! Toyota uses Just-in-Time inventory management to get parts only when needed. This reduces storage costs and waste, making their operations more efficient.
How does technology help in boosting operational efficiency?
Technology can automate repetitive tasks, integrate different systems, and provide data for better decision-making. This helps in making operations faster and more efficient.
What is the role of resource allocation in operational efficiency?
Allocating resources effectively ensures that the right amount of labor, equipment, and materials are used. This minimizes waste and maximizes productivity.
Why is it important to measure and scale efficiency initiatives?
Measuring helps you know what works and what doesn’t. Scaling successful initiatives allows the whole organization to benefit from localized improvements, making the entire operation more efficient.