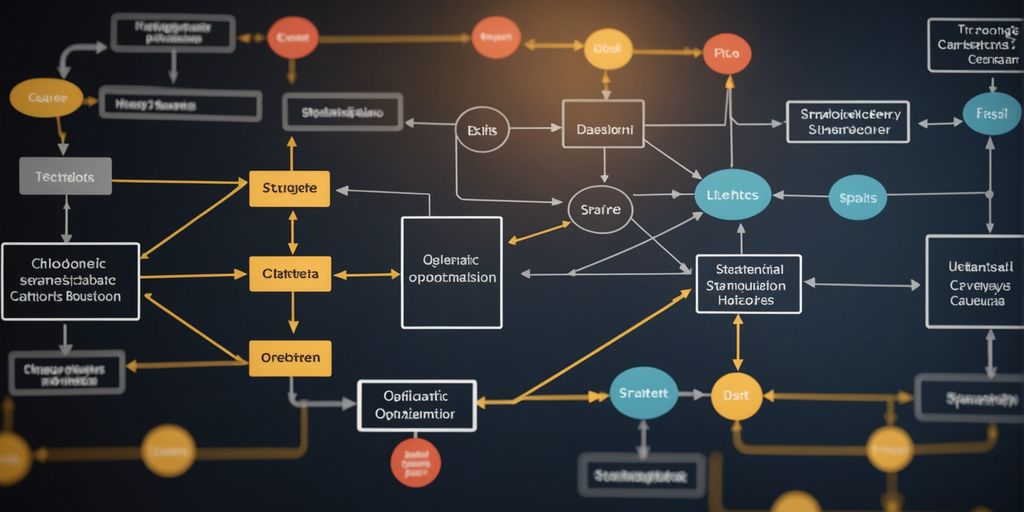
Maximizing Efficiency: A Comprehensive Guide to Strategic Process Optimization
In today’s fast-paced world, businesses need to be as efficient as possible to stay ahead. Strategic process optimization is a key tool that helps companies streamline their operations, cut costs, and boost productivity. This guide will walk you through the basics and provide actionable steps to make your processes more efficient.
Key Takeaways
- Strategic process optimization helps businesses streamline their operations and boost productivity.
- Identifying inefficiencies is the first step to improving any process.
- Using tools like Lean and Six Sigma can lead to significant improvements.
- Technology, including AI and IoT, plays a crucial role in modern process optimization.
- Continuous monitoring and employee training are essential for sustaining efficiency.
Understanding the Fundamentals of Strategic Process Optimization
Defining Strategic Process Optimization
Strategic process optimization is all about making our business processes better. Optimization is an iterative process that involves talking to the people it affects and making changes as you go. We aim to minimize costs and maximize efficiency without breaking any rules.
Key Principles and Concepts
There are a few key ideas we need to understand:
- Continuous Improvement: Always look for ways to make things better.
- Customer Focus: Keep the needs of the customer in mind.
- Data-Driven Decisions: Use data to guide our choices.
Importance in Modern Business
In today’s world, companies need to do more with less. By optimizing our processes, we can improve performance, boost customer satisfaction, and stay competitive. It’s a vital step in any organization’s journey to success.
Business process optimization is not just about cutting costs; it’s about improving efficiency and bottom-line results, helping companies thrive in the years ahead.
Identifying Inefficiencies in Existing Processes
Common Signs of Inefficiency
Recognizing inefficiencies is the first step to improvement. Identifying inefficient processes helps us focus our efforts where they matter most. Some common signs include frequent delays, high error rates, and redundant tasks. Regularly reviewing these signs can help us pinpoint areas needing attention.
Tools for Process Analysis
To find inefficiencies, we can use various tools. Process mapping and visualization help us see the entire workflow, making it easier to spot bottlenecks and unnecessary steps. Additionally, software tools can analyze data to highlight inefficiencies we might miss.
Case Studies of Inefficiency
Learning from others can be very helpful. Case studies show us real-world examples of inefficiencies and how they were fixed. These stories provide valuable insights and can guide us in our own process improvement efforts.
By understanding where inefficiencies exist, we can strategically prioritize our efforts and allocate resources to the areas that will have the greatest impact on efficiency.
Implementing Effective Process Improvement Strategies
Lean and Six Sigma Methodologies
Lean and Six Sigma are two popular methods for improving processes. Lean focuses on removing waste, while Six Sigma aims to reduce errors. Combining these methods can lead to significant improvements. We start by identifying the improvement opportunity, then obtain stakeholder buy-in, design the process improvement plan, test the changes, and finally, implement them.
Workflow Automation Tools
Using workflow automation tools can save time and reduce errors. These tools help automate repetitive tasks, allowing employees to focus on more important work. Some common tools include project management software, customer relationship management (CRM) systems, and enterprise resource planning (ERP) systems.
Change Management Techniques
Change management is crucial for successful process improvement. It involves preparing, supporting, and helping individuals and teams make organizational changes. By prioritizing clear communication and comprehensive training, we can overcome resistance and equip our workforce with the tools and knowledge necessary to embrace and implement process improvements.
Implementing process improvements is not a one-time task but an ongoing journey. We must continuously collect and analyze data on key performance indicators (KPIs) to ensure sustained efficiency.
Leveraging Technology for Process Optimization
Role of AI and Machine Learning
AI and machine learning are game-changers in process optimization. These technologies can analyze vast amounts of data quickly, identifying patterns and suggesting improvements. By automating routine tasks, we can free up human resources for more strategic activities. This not only boosts efficiency but also reduces the chances of human error.
Benefits of Cloud-Based Solutions
Cloud-based solutions offer flexibility and scalability that traditional systems can’t match. They allow us to access data and applications from anywhere, making it easier to manage processes remotely. Additionally, cloud solutions often come with built-in security features, ensuring that our data is protected. This means we can focus on optimizing processes without worrying about data breaches.
Integration of IoT in Process Management
The Internet of Things (IoT) is revolutionizing process management by providing real-time data and insights. IoT devices can monitor equipment, track inventory, and even predict maintenance needs. This level of monitoring helps us identify inefficiencies and address them before they become major issues. With IoT, we can achieve a level of process optimization that was previously unimaginable.
Streamlining processes is a continuous effort that requires ongoing monitoring and improvement. By regularly reviewing and optimizing processes, organizations can achieve and maintain optimal efficiency.
Monitoring and Sustaining Process Efficiency
To keep our processes running smoothly, we need to keep an eye on them and make sure they stay efficient. This means we have to check how things are going all the time and make small changes when needed. Achieving and sustaining process stability requires a comprehensive approach that encompasses continuous monitoring, improvement, and a culture that fosters growth.
Maximizing ROI Through Strategic Process Optimization
Investing in business process optimization can significantly boost our bottom-line results. By streamlining operations and maximizing productivity, we can increase revenue and position our company to thrive in the years ahead. Identifying cost-saving opportunities is a fundamental aspect of reducing expenses and maximizing ROI. Start by analyzing current operations and expenses to find areas for improvement.
Case Studies of Successful Process Optimization
In the manufacturing sector, process optimization has led to significant improvements. For instance, a major automotive company revamped its assembly line, reducing production time by 20%. This change not only cut costs but also improved product quality. By implementing business process optimization, organizations can increase productivity, reduce costs, and improve customer satisfaction.
Healthcare providers have also benefited from process optimization. A large hospital system streamlined its patient intake process, which reduced wait times by 30%. This improvement not only enhanced patient satisfaction but also allowed the hospital to serve more patients efficiently.
In other words, business process optimization radically redesigns existing processes and workflows, helping eliminate waste and elevate best practices.
In the financial services industry, a leading bank optimized its loan approval process. By automating several steps, the bank reduced the approval time from weeks to just a few days. This not only improved customer experience but also increased the number of loans processed, boosting the bank’s revenue.
Explore our case studies to see how we’ve helped businesses like yours optimize their processes and achieve remarkable success. Ready to transform your business? Visit our website to learn more and get started today!
Conclusion
In conclusion, optimizing business processes is essential for any organization aiming to boost efficiency and achieve long-term success. By identifying inefficiencies, streamlining workflows, and leveraging technology, companies can significantly improve their operations. Remember, this is not a one-time task but an ongoing effort that requires regular monitoring and adjustments. Investing in process optimization not only cuts costs but also enhances productivity, customer satisfaction, and profitability. Start today and pave the way for a more efficient and successful future.
Frequently Asked Questions
What is strategic process optimization?
Strategic process optimization is improving a business process to make it more efficient. This involves analyzing current workflows, identifying areas of waste, and implementing changes to enhance productivity.
Why is process optimization important for businesses?
Process optimization is crucial because it helps businesses save time and money. By making processes more efficient, companies can reduce costs, improve customer satisfaction, and boost overall performance.
What are some common signs of inefficiency in a process?
Common signs include frequent delays, high error rates, and excessive costs. If a process takes longer than expected or requires too many resources, it may need optimization.
How can technology help in process optimization?
Technology can automate repetitive tasks, provide real-time data for better decision-making, and streamline workflows. Tools like AI, machine learning, and cloud-based solutions can significantly enhance process efficiency.
What is the role of employee training in maintaining process efficiency?
Employee training is vital for sustaining process efficiency. Well-trained employees understand the processes better and can identify and address inefficiencies quickly. Continuous training ensures everyone is up-to-date with the latest best practices.
What are some effective strategies for process improvement?
Effective strategies include using Lean and Six Sigma methodologies, implementing workflow automation tools, and applying change management techniques. These approaches help in systematically identifying and eliminating inefficiencies.